Exploration diamond drilling
Exploration diamond drilling is used in the mining industry to probe the contents of known ore deposits and potential sites. By withdrawing a small diameter core of rock from the orebody, geologists can analyse the core by chemical assay and conduct petrologic, structural and mineralogical studies of the rock.
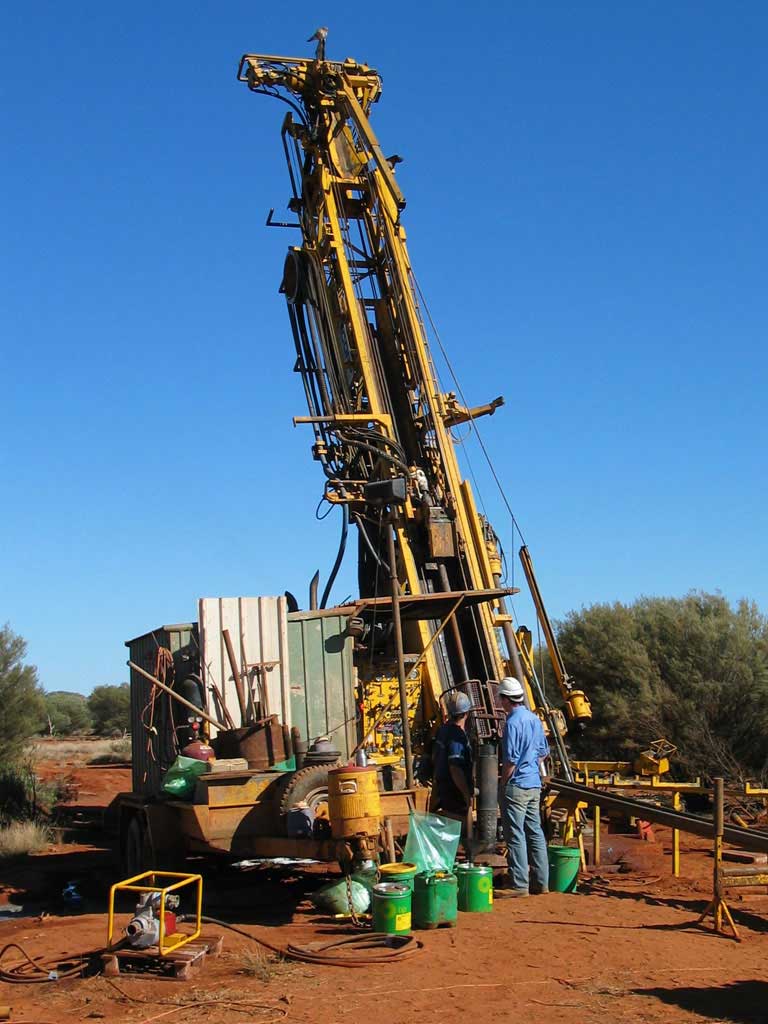
History
Rodolphe Leschot is often cited as being the inventor of the first core bit in 1863. Early diamond drilling opened up many new areas for mineral mining, and was related to a boom in mineral exploration in remote locations. Before the invention of the portable diamond drill, most mineral prospecting was limited to finding outcrops at the surface and hand digging. In the late 1970s, General Electric pioneered the technology of polycrystalline diamond compacts (PDCs) as a replacement for natural diamonds in drill bits.
Diamond drilling
Exploration diamond drilling differs from other geological drilling in that a solid core is extracted from depth, for examination on the surface. The key technology of the diamond drill is the actual diamond bit itself. It is composed of industrial diamonds set into a soft metallic matrix. As shown in the figure, the diamonds are scattered throughout the matrix, and the action relies on the matrix to slowly wear during the drilling process, so as to expose more diamonds. The bit is mounted onto a core barrel which is attached to the drill stem, which is connected to a rotary drill. Water is injected into the drill pipe, so as to wash out the rock cuttings produced by the bit and also to reduce the heat produced due to friction which causes less wear and tear of the bits. An actual diamond bit is a complex affair, usually designed for a specific rock type, with many channels for washing. The drill uses a diamond encrusted drill bit to drill through the rock. The drill produces a "core" which is photographed and split longitudinally. Half of the split core is assayed while the other half is permanently stored for future use and re-assaying if necessary. Although a larger diameter core is the most preferred it is the most expensive. The most common diameter sizes of core are NQ and CHD 76.
Core extraction
Merely advancing the drill by rotary action (and washing) causes a core to be extracted inside the barrel as shown. However, at a depth of perhaps 300 m, there must be a way to retrieve the core and take it to the surface. Constantly withdrawing the entire heavy drill pipe is impractical, so methods were developed to pull up the core inside the barrel. If the rock would always be solid granite, and the core would always break at the drill bit, then it would be a simple matter to stop the drilling, and lower a simple grabbing device by a wire and pull up the core. Unfortunately, many applications require an undisturbed core in fractured rock, which calls for elaborate wire-line devices. The photo shows the extraction of a core, using a triple-tube wire-line system, capable of extracting core under the worst conditions. This is very important when exploring fault zones such as the San Andreas Fault.
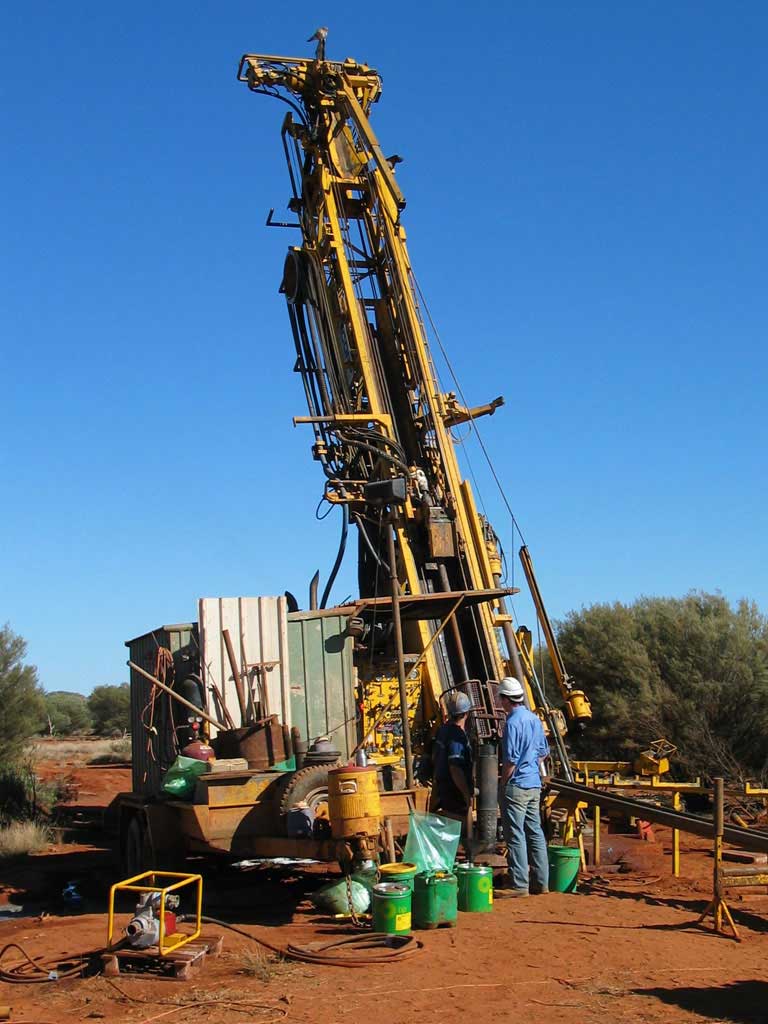
History
Rodolphe Leschot is often cited as being the inventor of the first core bit in 1863. Early diamond drilling opened up many new areas for mineral mining, and was related to a boom in mineral exploration in remote locations. Before the invention of the portable diamond drill, most mineral prospecting was limited to finding outcrops at the surface and hand digging. In the late 1970s, General Electric pioneered the technology of polycrystalline diamond compacts (PDCs) as a replacement for natural diamonds in drill bits.
Diamond drilling
Exploration diamond drilling differs from other geological drilling in that a solid core is extracted from depth, for examination on the surface. The key technology of the diamond drill is the actual diamond bit itself. It is composed of industrial diamonds set into a soft metallic matrix. As shown in the figure, the diamonds are scattered throughout the matrix, and the action relies on the matrix to slowly wear during the drilling process, so as to expose more diamonds. The bit is mounted onto a core barrel which is attached to the drill stem, which is connected to a rotary drill. Water is injected into the drill pipe, so as to wash out the rock cuttings produced by the bit and also to reduce the heat produced due to friction which causes less wear and tear of the bits. An actual diamond bit is a complex affair, usually designed for a specific rock type, with many channels for washing. The drill uses a diamond encrusted drill bit to drill through the rock. The drill produces a "core" which is photographed and split longitudinally. Half of the split core is assayed while the other half is permanently stored for future use and re-assaying if necessary. Although a larger diameter core is the most preferred it is the most expensive. The most common diameter sizes of core are NQ and CHD 76.
Core extraction
Merely advancing the drill by rotary action (and washing) causes a core to be extracted inside the barrel as shown. However, at a depth of perhaps 300 m, there must be a way to retrieve the core and take it to the surface. Constantly withdrawing the entire heavy drill pipe is impractical, so methods were developed to pull up the core inside the barrel. If the rock would always be solid granite, and the core would always break at the drill bit, then it would be a simple matter to stop the drilling, and lower a simple grabbing device by a wire and pull up the core. Unfortunately, many applications require an undisturbed core in fractured rock, which calls for elaborate wire-line devices. The photo shows the extraction of a core, using a triple-tube wire-line system, capable of extracting core under the worst conditions. This is very important when exploring fault zones such as the San Andreas Fault.
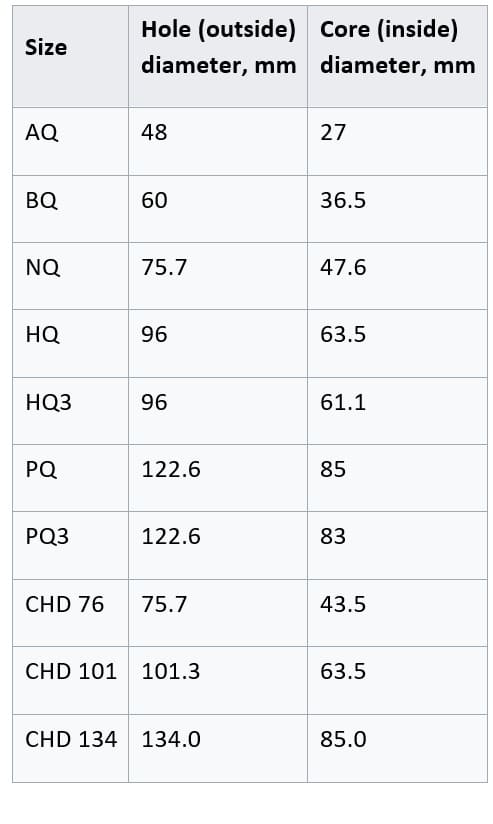
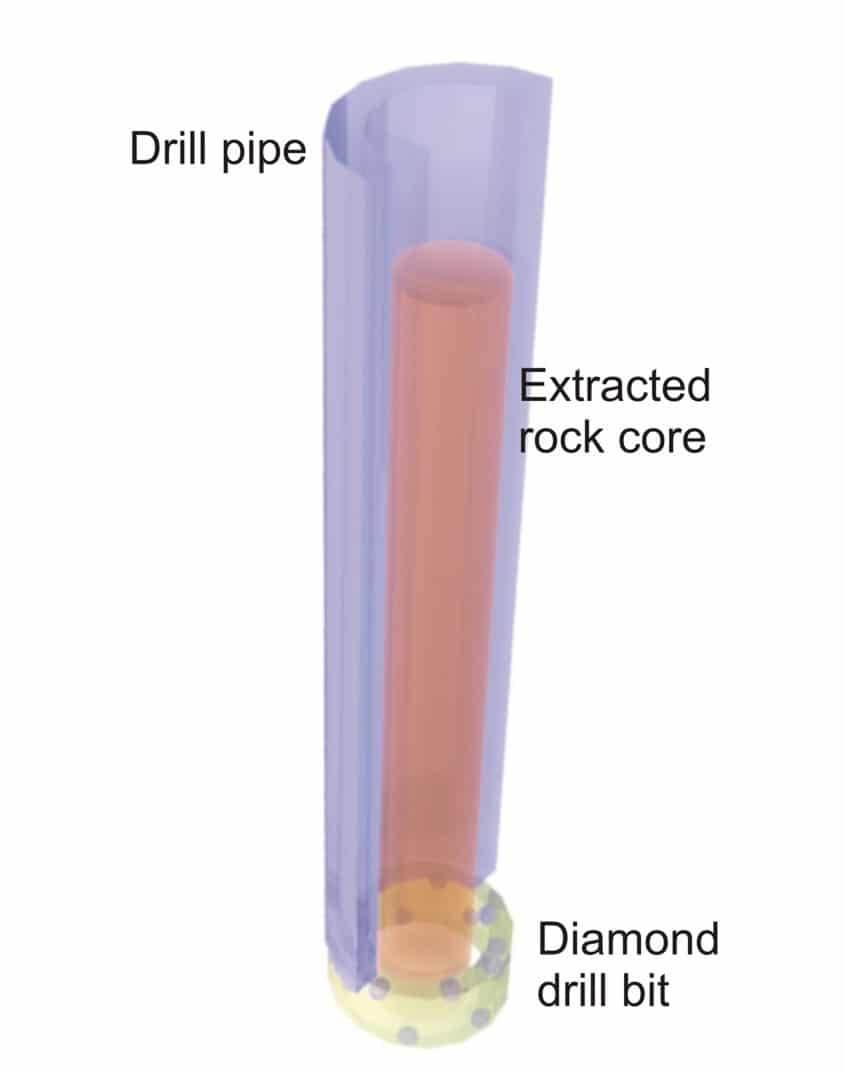
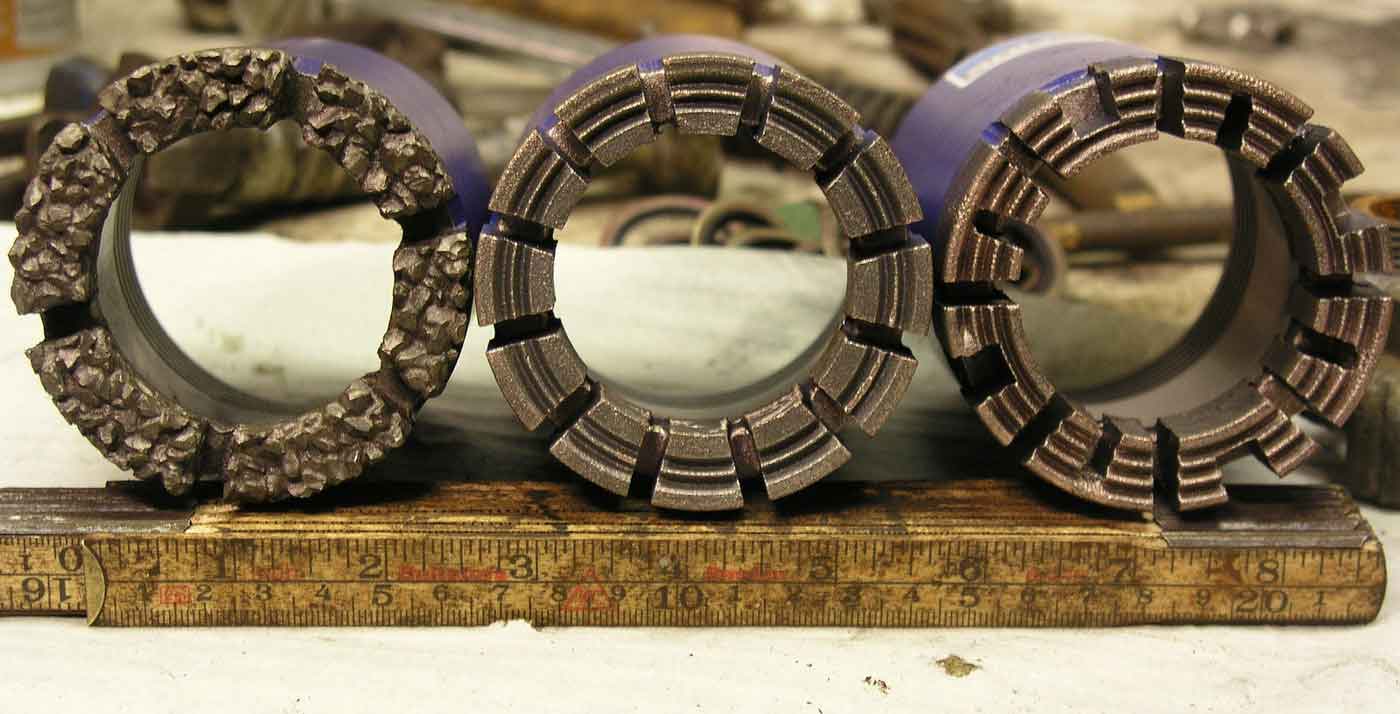
DRILL RIGS
Building on the solid legacy of proven designs, today's Cat® Rotary Blasthole Drills offers substantial technology, efficiency and productivity improvements to efficiently reach your targeted productivity rates. Our newest models fully integrate Cat designs, components and technologies, and every model delivers exactly what you expect from a product bearing the Cat brand: durability, precision, productivity, and unmatched parts and service support, anywhere in the world. It's what lies beneath the paint that counts — that's where you'll find everything we stand for.
MD6200
The MD6200 is our smallest drill, and it has the smallest shipping envelope of any drill in its class. In addition, it can be transported over the road with the mast on, so it can simply roll onto a truck when it’s time to move to another site. It also offers best-in-class maneuverability. Its compact working envelope allows it to get it into position faster, reducing the time spent accessing drill patterns and moving between holes. Its oversized Cat 336 excavator-style undercarriage provides best-in-class tractive effort and drawbar pull, and stands up to the toughest conditions on your site. The MD6200 cab offers the comfort and control you expect from a Cat machine, with ergonomic controls that help your operator stay alert and avoid fatigue. And optional upgrades — like a heated, ventilated seat with heavy-duty suspension and dual-pane glass —help operators stay comfortable all shift long.
Multifunction joystick controls and touchscreens are easy and intuitive to use, and three standard cameras give your operators excellent visibility.
The MD6200 is controlled through proven Cat electronics, with an electronic architecture your technicians are familiar with from other Cat machines. Integrated machine protection features and interlocks help keep your operators safe, and the machine up and running by preventing potential failures or misuse.
With Cat Electronic Technician (Cat ET), troubleshooting is quick and easy. The MD6200’s electronics also provide a common platform for the integration of a number of future autonomy solutions.
BIT LOAD
UP TO 16 964 KG (37,400 LB)
HOLE DIAMETER
UP TO 127-200 MM (5.0-7.87 IN)
ENGINE
C18® ACERT™ @ 1,800 RPM
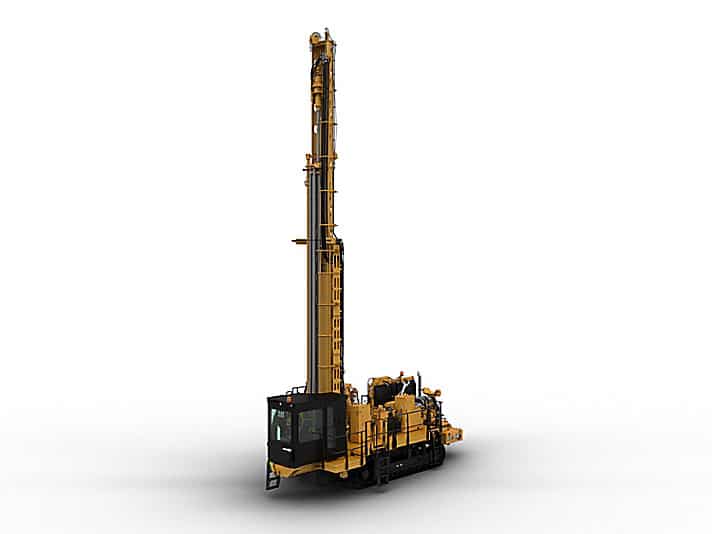
MD6640
Designed for longevity and easy access to components, the MD6640 is favored by drillers for dependability and serviceability. Adding to its productivity are smart features such as a simple hydraulics system, reliable electrical in all weather conditions, quick pipe changes, and angle hole drilling to 25° in 5° increments. Efficient and comfortable cab is designed for maximum operator productivity. Additionally, vibration and noise are minimized by the use of proven programmed drill control option with the cushioned centralizer and shock sub.
BIT LOAD
UP TO 64 000 KG (UP TO 141,096 LB)
HOLE DIAMETER
244 - 406 MM (9.6 - 16 IN)
ENGINE
AC INDUCTION MOTOR - DUAL SHAFT 522-746 KW (600 HP)
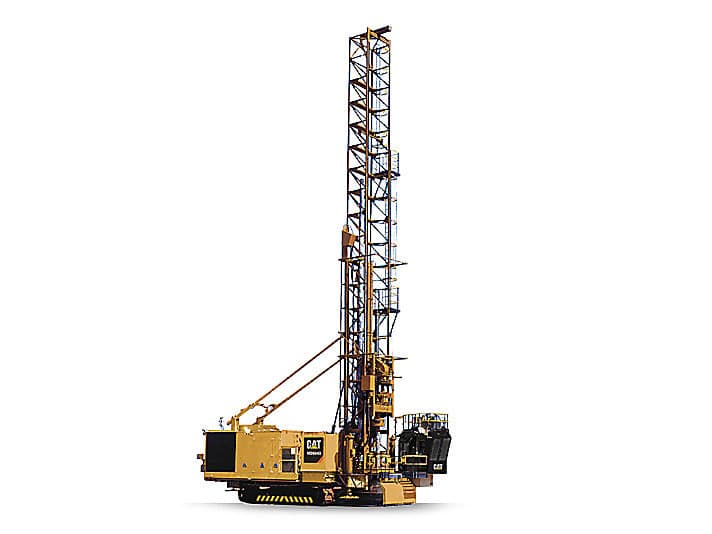
MD6250
The Cat® MD6250 rotary drill is built from the ground up with 100 percent Cat parts to help you get the most out of your operation. With built-in autonomous features and the option to integrate Cat MineStar technologies, the MD6250 offers accurate, reliable performance in any hard rock drilling application. The MD6250 is controlled through proven Cat electronics, with an electronic architecture your technicians are familiar with from other Cat machines. Integrated machine protection features and interlocks help keep your operators safe, and the machine up and running by preventing potential failures or misuse.
With Cat Electronic Technician (Cat ET), troubleshooting is quick and easy. The MD6250’s electronics also provide a common platform for the integration of a number of future autonomy solutions.
Technology and automation is foundational in MD6250 to enhance operational performance. MD6250 delivers drill assist functions, semi-autonomous / autonomous features and machine health reporting, all of which improve drilling efficiencies and results. The MD6250 matched powertrain delivers performance and fuel consumption benefits thru electronic control strategies. Variable volume air control allows drillers to match compressor output to specific application and drill tooling.
The MD6250 powertrain is optimized with a high powered engine and largest “standard” compressor in class for fast cycle times and its designed to withstand the rigors of drilling applications.
BIT LOAD
UP TO 32 655 KG (UP TO 71,993 LB)
HOLE DIAMETER
UP TO 152-250 MM (UP TO 6-9.8 IN)
ENGINE
C27 ACERT™ @ 1,800 RPM
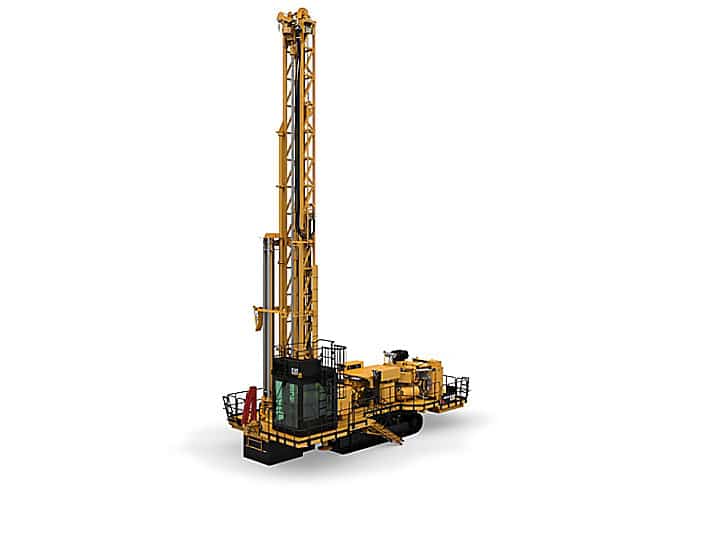
MD6310
Combine a 100% Caterpillar design with exclusive, integrated technology options and what do you get? Up to four times greater pattern accuracy. With the new Cat® MD6310 rotary blasthole drill, you choose the level of automation you need to ensure every hole is placed and drilled to plan every time. It’s precision performance that drives down your costs and and drives up your profitability.
BIT LOAD
UP TO 42 149 KG (UP TO 92,922 LB)
HOLE DIAMETER
203-311 MM (8-12.25 IN)
ENGINE
C32® @ 1,800 RPM
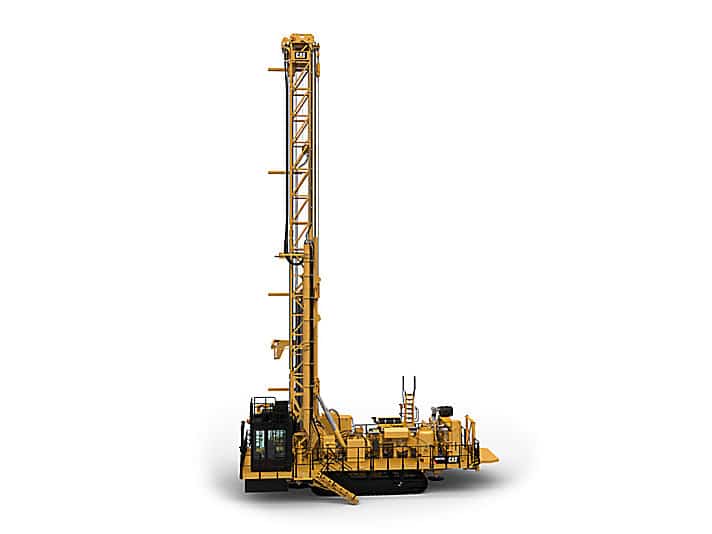
MD6540C
MD6540C Rotary Blasthole Drill 16 or 20 m (52.5 or 65.6 ft) Mast Configuration
BIT LOAD
UP TO 53 845 KG (UP TO 118,719 LB)
HOLE DIAMETER
229-406 MM (9-16 IN)
ENGINE
CAT® 3512C HD
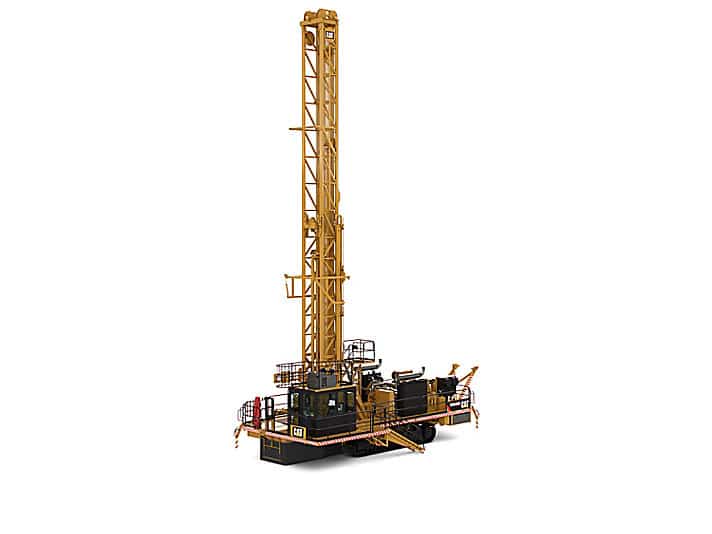